Energy from Waste plants are becoming more and more popular for disposing of our waste. Their construction have seen a huge growth over the last decade and the best way to maintain them? Hydrodemolition.
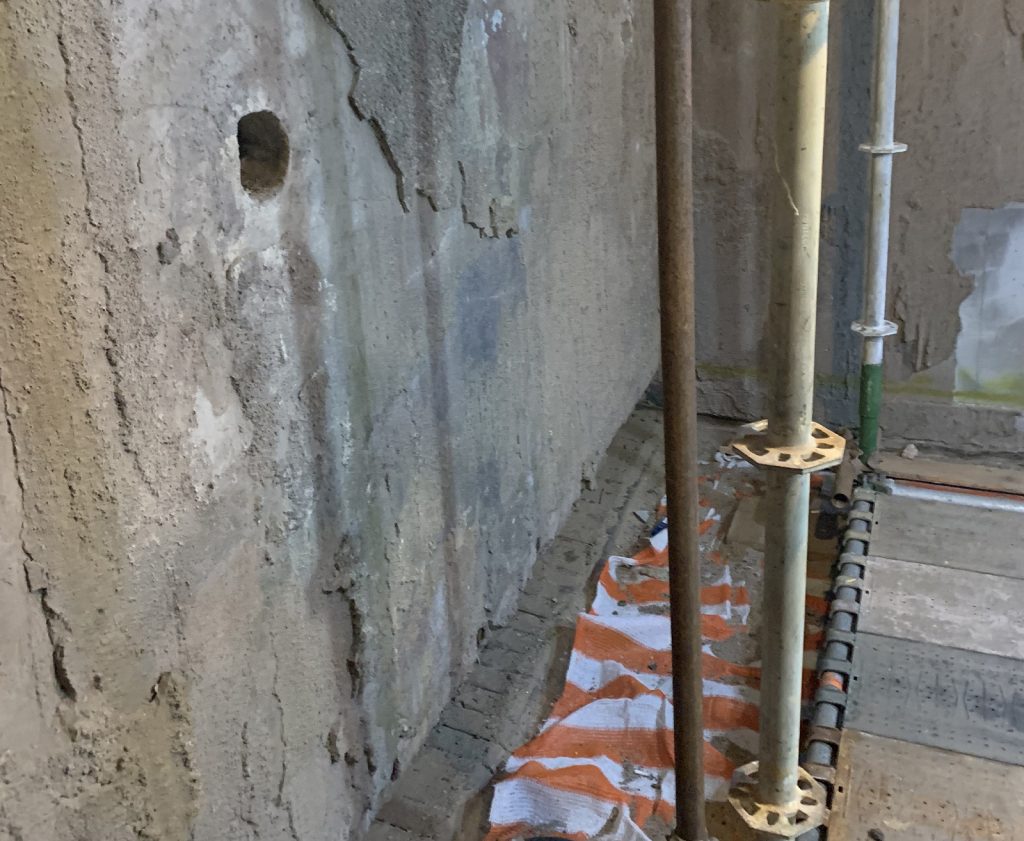
In 2006, 3.3 million tonnes of UK waste was incinerated. Due to the concrete walls in the incinerator they are difficult to demolish by conventional means. They are perfect for Hydro Demolition.
According to recent data, Incineration will account for more than half of all disposal. This is due to taxes being introduced on disposing of waste at landfill.
There are now 44 incinerators across the UK in operation, which has risen from 31 since 2013. There are currently plans for over 100 new incinerators
The 44 waste incinerators across the UK burned 10.9 million tonnes of waste last year. This accounted for 42 per cent of rubbish disposal.
To keep up with growing demand 16 new plants are currently under construction across the UK.
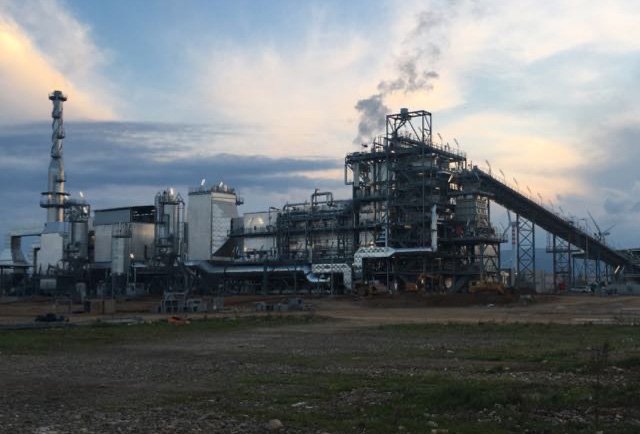
EfW plants & incinerators are used all over the world.
The Italian Job by Hydroblast
Hydroblast received a call from a customer last September and within 1 week, flights were booked to Cagliari, in Sardinia.
Details of the job were discussed that evening upon arrival. With us flying back the next morning.
The Friday of that week saw the 1100 mile trip towards Sardinia begin. The total trip took 3 days across the scenic Alps.
The scenery during the drive did not disappoint with stunning views of the Alps in Southern France and Italy.
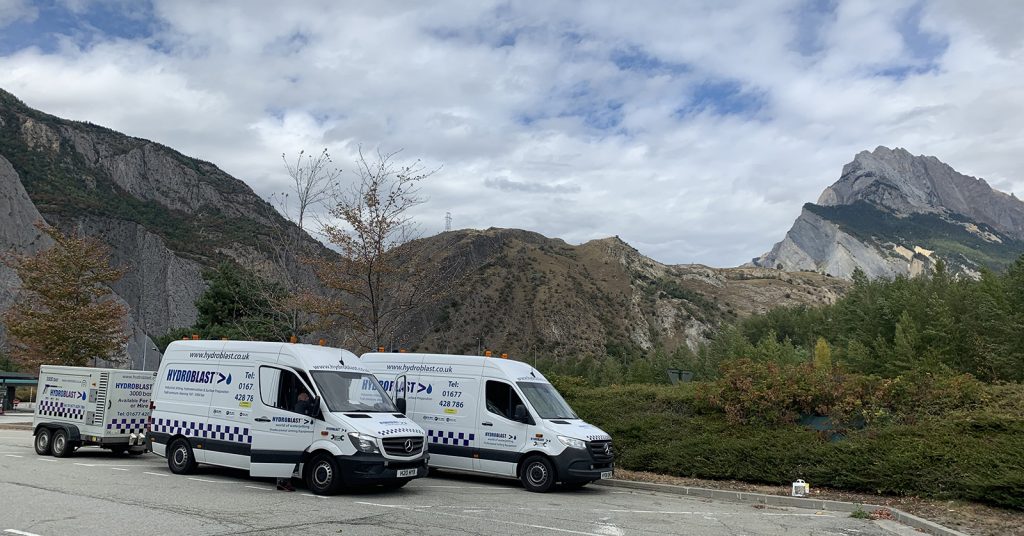
Why is refractory removal necessary?
Energy-from-waste plants (EfW) produce intense heat through combustion and overtime this heat damages the refractory lining of the incinerator.
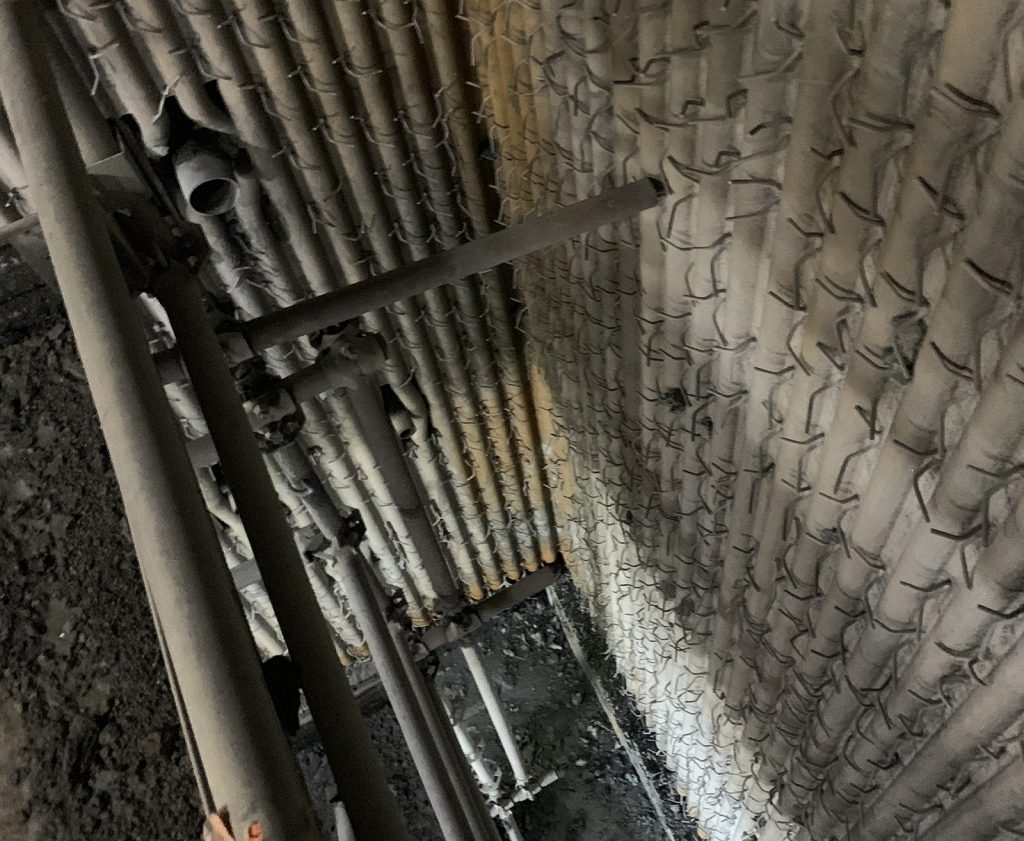
As a result of extreme heat inside the fire chamber, the cement starts to break and burn out. This broken cement then needs to be removed but without damaging the hot water pipes that are covered with refractory.
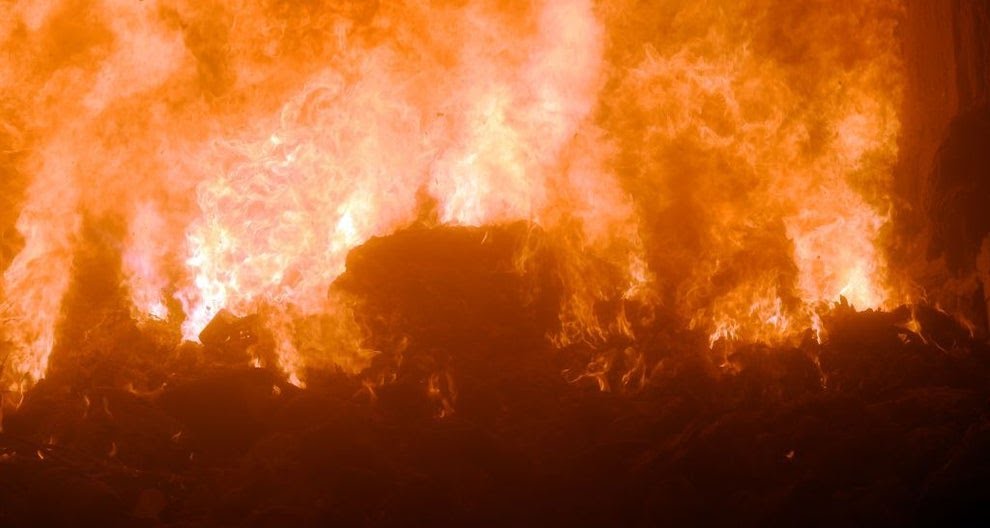
Using conventional methods such as a hammer and chisel runs the risk of the chisel puncturing, or even bursting, the water pipe. If this happens, there is a considerable downtime, the cost of cutting out the damaged pipe, the cost of welding in new pipe, x-raying the welds to confirm that they are correct, and then having to pressure test the pipe with water in to check for any leaks.
Although using the technique of Hydro demolition to remove refractory cement/lining is more expensive than labourers and traditional jack hammer methods, there is no comparison in cost savings due to the speed of removal and guaranteed no tube damage.
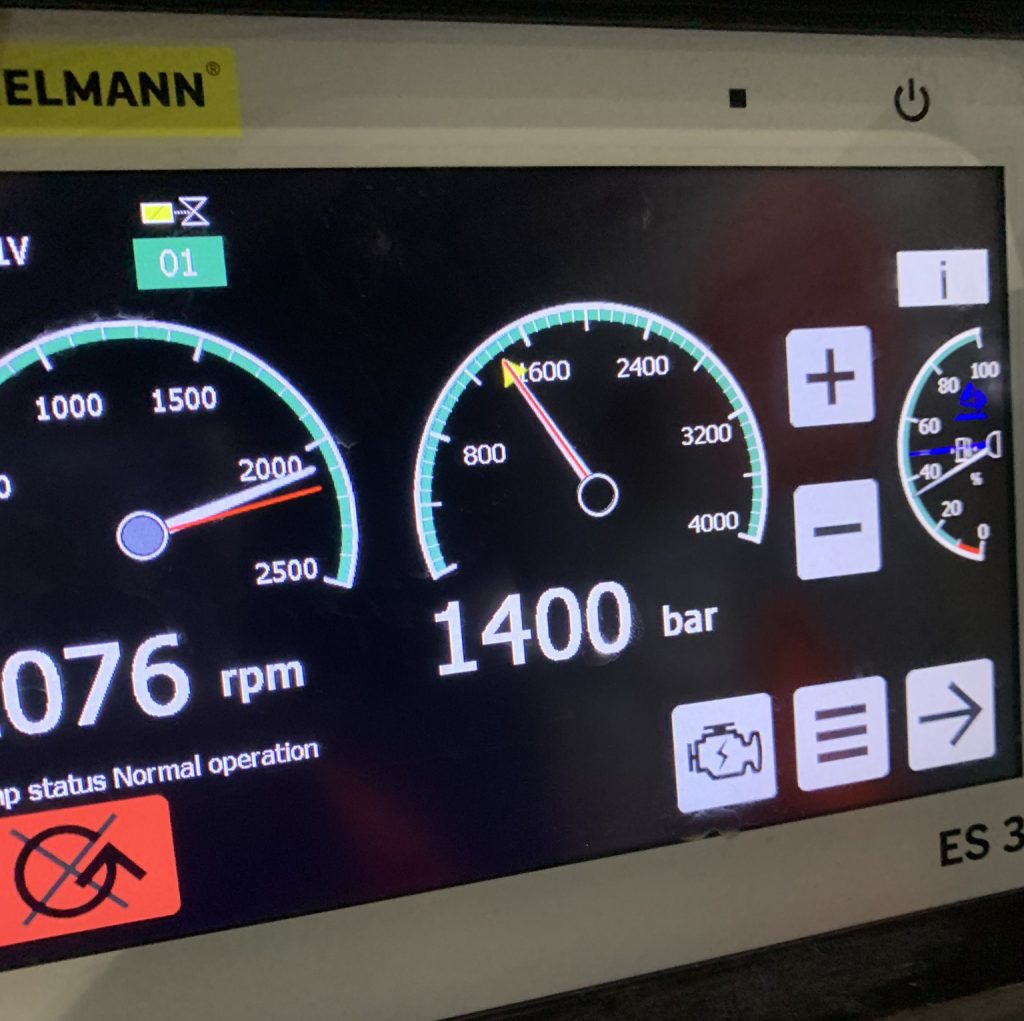
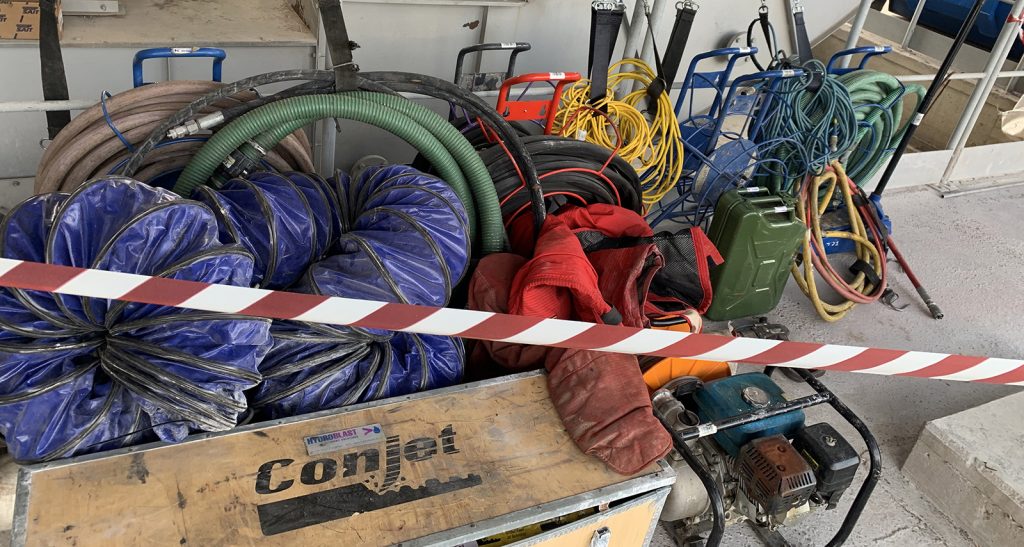
What did the job involve?
Hydroblast required breaking out of 90m2 in a critical time scale which involved running robotic and hand lance equipment in tandem operation.
After the first week was under our belt it was clear the operation needed to be sped up which involved running 2 units 24 hours a day for the next week and a half solidly.
The units were 2 brand new Hammelmann pumps 1400 bar @ 78LPM and 2800 bar hand lancing with flows available up to 25LPM.
German built quality meant the units never missed a beat and were very reliable.
The larger high pressure pump was connected to a Conjet Nalta frame which is quick and easy to assemble in small spaces.
Conjet is one of our Robotic suppliers based in Sweden.
The equipment was under harsh conditions throughout the project, and required additional spares. The service direct from the factory was first class with next day weekend delivery.
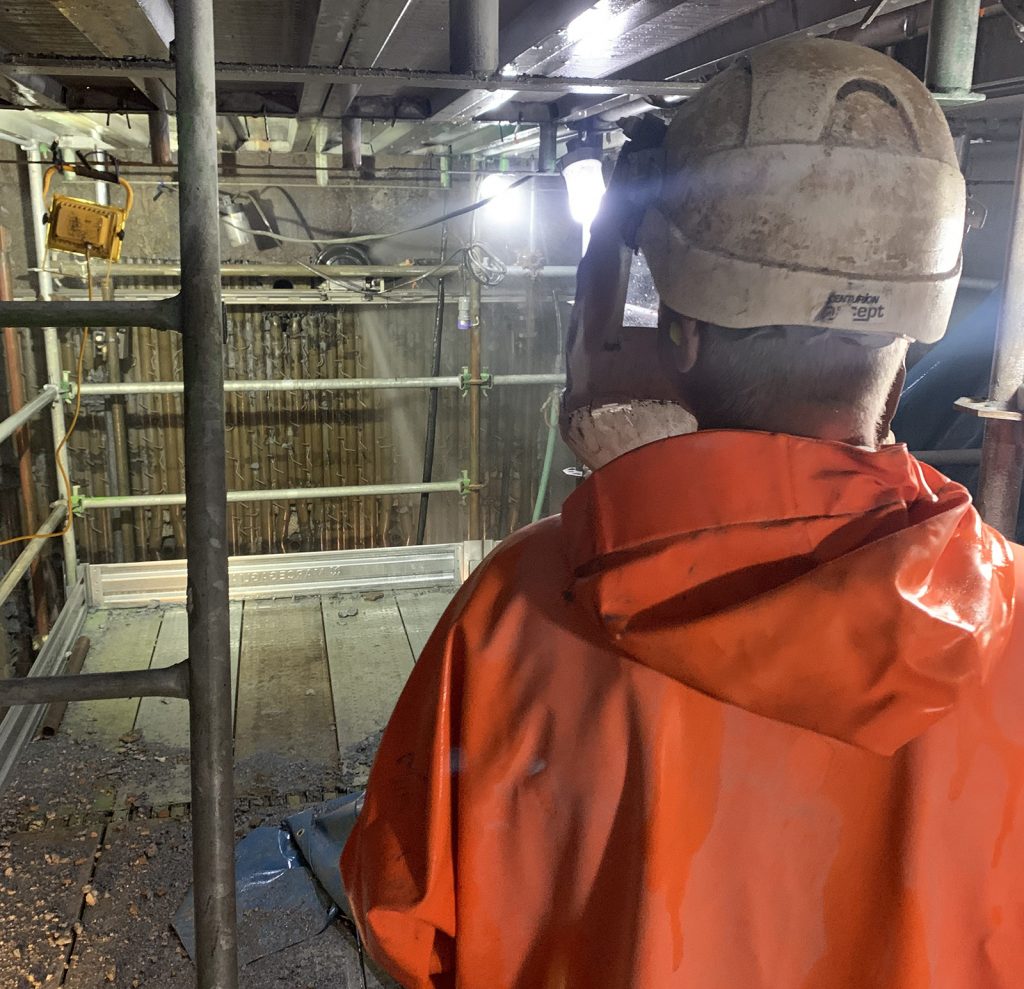
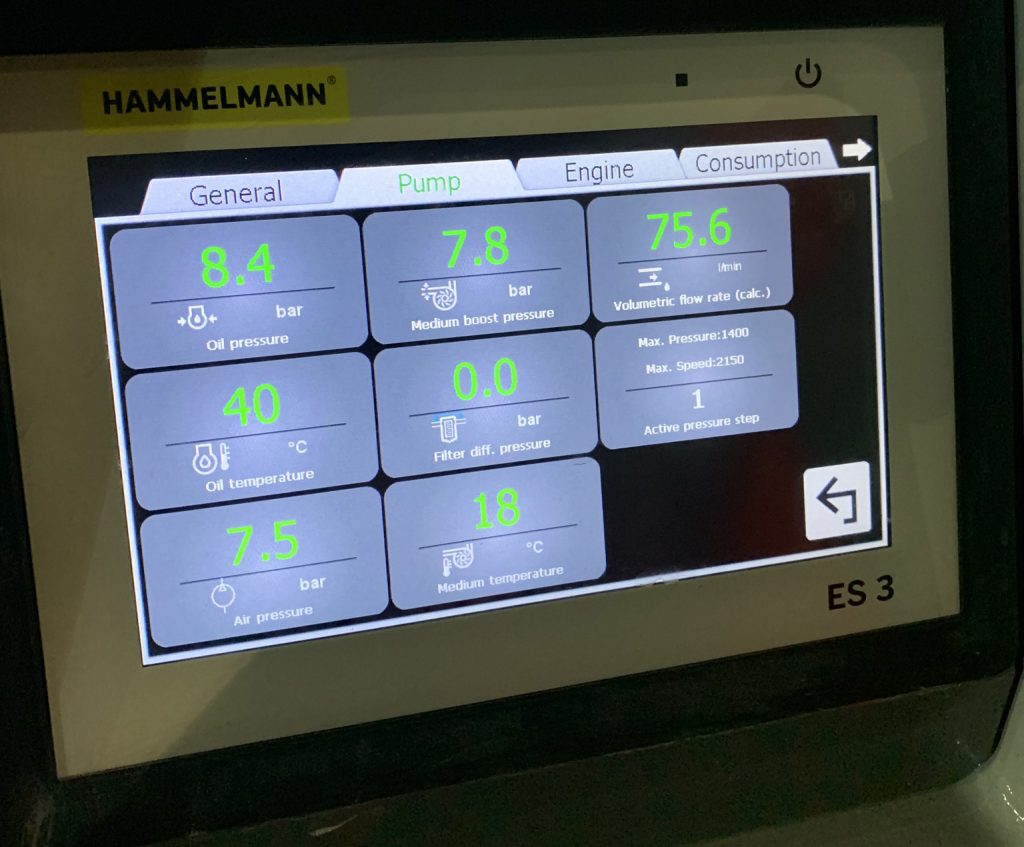
Why choose Hydroblast Hydro Demolition?
– No risk of damaged tubes
– Cost efficient with less down time
– Safe and effective
– up to 10 times faster than traditional techniques
– Fitted equal distance system ensures there is a consistent distance between nozzle and surface to ensure a consistent power and reduced energy wastage
– Power control module permits operators to work at a safe distance by controlling the robot wirelessly

We were away for three weeks and would like to thank our staff for their hard work. They completed the job safely and successfully.
Operations Director Ross McDonald who managed the project commented.
“The job couldn’t have been completed without the willingness and dedication of the team. They are a credit to not just us but themselves. There were some minor issues on site but the team worked together and overcame them. The deadline was met making for a very happy client. A great deal was learned, and I think everyone came away from the job feeling proud of their achievements and rightly so. The weather certainly helped with three weeks of low forty degrees C. Significant investments for 2020 have already been purchased and further are in the pipeline for further international work that’s scheduled this year, keep following for updates.”
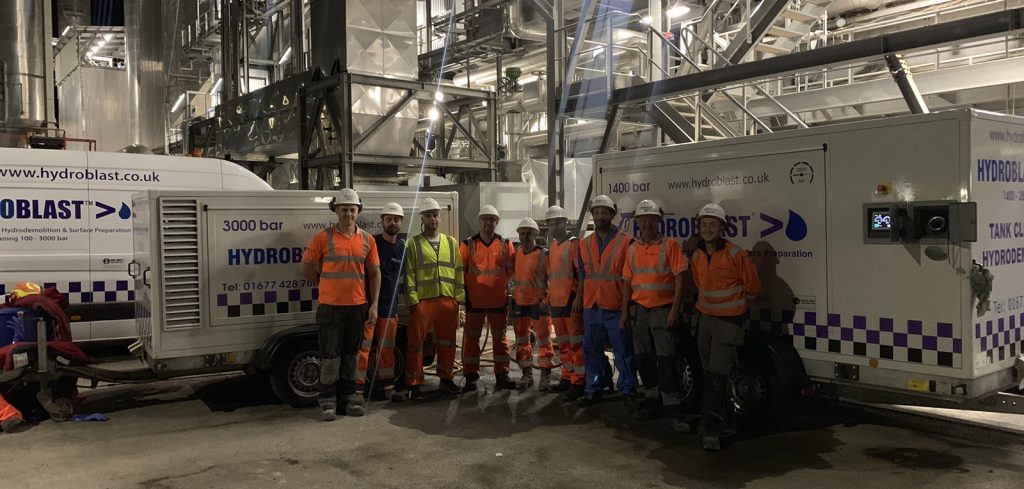